Outerra forum
- July 15, 2025, 06:21:22 pm
- Welcome, Guest
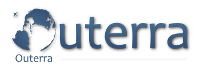
News:
Download Outerra Tech Demo. Unofficial Outerra Discord server, MicroProse Discord server for OWS.
Download Outerra Tech Demo. Unofficial Outerra Discord server, MicroProse Discord server for OWS.