Outerra forum
- July 05, 2025, 11:26:17 pm
- Welcome, Guest
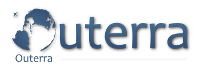
News:
Download Outerra Tech Demo. Unofficial Outerra Discord server, MicroProse Discord server for OWS.
Download Outerra Tech Demo. Unofficial Outerra Discord server, MicroProse Discord server for OWS.